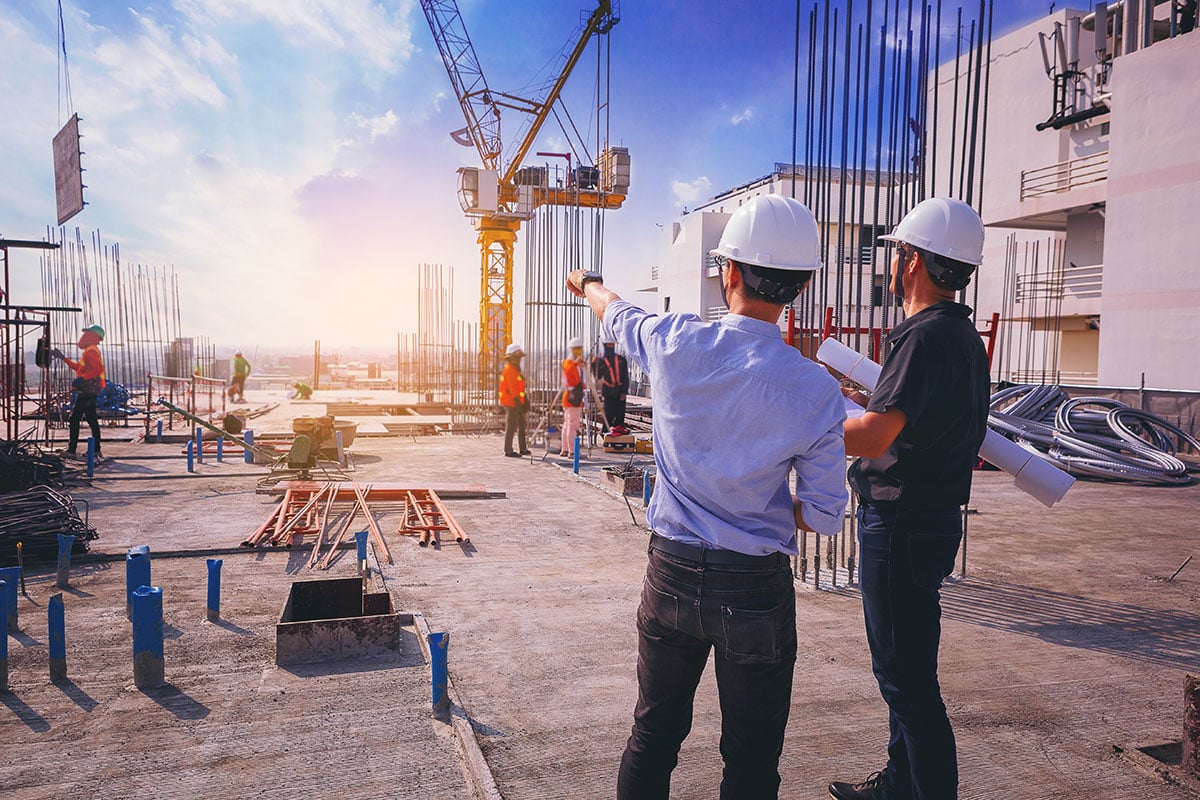
Roof and wall systems, exterior doors, windows, and below-grade systems form a building’s envelope. These systems protect occupants from external environmental forces, such as wind, sun, rain, and snow, and help balance and control the internal environment.
Inadequate waterproofing of the building enclosure exposes occupants to health risks while gambling with a structure’s overall performance and longevity. Water-related damage above ground is more noticeable for fixing to prevent further deterioration of a structure; similar issues below grade can go undetected for a very long time.
Key stakeholders must find proactive ways to protect below-grade elements during a building’s planning, development, and construction phases to prevent the need for expensive repairs. Let’s explore the risks of inadequate waterproofing below grade and the products and solutions available to help prevent or halt future water damage.
Why Below-Grade Systems Need Proper Design and Waterproofing
Careful consideration is needed to design below-grade enclosure systems to prevent common issues related to poor performance. The structural integrity of any building elements below ground can become compromised when exposed to weathering, foot traffic, thermal effects, moisture build-up, or water leaks.
Below-grade structural waterproofing is necessary for preventing costly water damage to any part of the building below ground level, including foundation walls, below-grade plaza decks or basements, and shallow building foundations like slab-on-grade foundations.
Buildings in low-lying areas close to swamps, flood plains, rivers, and lakes are especially susceptible to water infiltration and moisture damage.
Common issues related to below-grade moisture build-up or water damage include:
- Efflorescence or crystalline salt deposits that form in basements, on floors, or crawlspace walls
- The development of structurally damaging mold
- Cracks in walls, or walls that bow inwards or outwards due to hydrostatic pressure
- Strange and unpleasant smells in basements or crawlspaces
- Decay and corrosion of steel embedded in concrete slabs
Top Challenges for Repairing Below Grade Systems
Unlike the rest of the building envelope, below-grade structures are not frequently replaced or easily accessed for repairs; they are usually designed to last a building’s approximate lifespan.
Water intrusion and moisture damage below grade can go unnoticed until it affects the building’s structural integrity, air quality, or indoor humidity levels. Excavating below grade for repairs is costly, so appropriate moisture protection of subsurface building components during construction is needed to prevent water intrusion, leakage, and drainage issues that lead to building deterioration.
A range of below-grade waterproofing products and systems have been developed to seal the building envelope properly, protect its structural integrity and minimize the need for expensive maintenance and repairs.
An Overview of Below Grade Waterproofing Systems
Properly waterproofing a building’s foundation is critical to the success of a structure. A below-grade waterproofing system protects structures against water infiltration. It consists of interacting waterproofing components that help prevent water intrusions and lateral water migration, including:
- Waterproofing membranes
- Protection, drainage, and insulation courses
- Water stops
- Expansion and control joints
- Flashings and counter flashings
- And overburden such as cast concrete, pavers, and wire mesh or rebars
Different Waterproofing Application Types
Waterproofing products can be applied to the exterior (or positive side) of a building’s subsurfaces, a building’s interior (or negative side) subsurfaces, or beneath a building’s structural slabs (its blind side).
These products are either post-applied (applied after foundational walls and floors have been poured) or pre-applied before the walls or floors have been built.
Positive Side Waterproofing
Positive side waterproofing products are post-applied on external building surfaces to prevent groundwater or surface water from infiltrating a building’s interior. This approach is appropriate when below-ground structures can be readily accessed and waterproofed from the outside.
Examples of positive side waterproofing products include vapor barriers, fluid-applied membranes, single-ply membranes, hot-applied bitumen systems, bentonite clay, and reinforced sheet-membrane systems. In addition, protection boards or insulation layers are installed over waterproofing membranes to protect the membrane from mechanical damage that can occur during backfilling.
Negative Side and Blind-Side Waterproofing
When ready access to below-grade building elements is not feasible, negative or blind-side waterproofing is required. Negative-side waterproofing is post-applied to internal building surfaces to stop water from reaching a building’s interior. Blind-side waterproofing is pre-applied between the ground and the underside of structural slabs to help seal and protect the foundation from water intrusion.
Horizontal and Vertical Waterproofing Applications
While vertical waterproofing is used to seal vertical wall envelopes above and below grade, horizontal waterproofing is needed for underground structures, such as basements and tunnels made from horizontal concrete or mud slabs. Horizontal waterproofing applications are also required when horizontal slabs are used as roofs for below-grade parking decks.
Polyglass’ Below-Grade Waterproofing Products
Polyglass’ complete range of superior below-grade waterproofing products and systems covers all structural waterproofing specifications and requirements, including waterproofing for decks, plazas, and elevated decks.
Our waterproofing solutions for the building envelope now include pre-applied and vertical blind-side waterproofing, post-applied foundation wall waterproofing, waterproofing primers, and accessories.
Polyglass Below-Grade Waterproofing Membranes
Pre-applied: Mapeproof™ AL PRO is a pre-applied, fully bonded HDPE waterproofing membrane that is ideal for horizontal slabs and vertical blind-side applications. Mapeproof AL PRO bonds integrally to poured concrete, forming an adhesive bond, and is designed to protect below-grade structures from water intrusion and lateral water migration.
Post-applied: Mapethene™ LT60 and Mapethene™ HT60 are post-applied self-adhered waterproofing membranes for below-grade structures and elevated decks. Mapethene LT60 is ideal for low-temperature applications (between 25°F – 60°F / -4°C – 16°C), while Mapethene HT60 is suitable for installations where the ambient temperature is above 40°F (5°C). Both membranes are cold applied without using flames.
Below-Grade Solvent and Water-Based Waterproofing Primers
Self-adhering waterproofing membranes require compatible surface primers to stick the membrane in place. Polyglass offers solvent- and water-based adhesive primers with our Mapethene LT60/HT60 waterproofing membranes.
Solvent-based: Mapeprime™ 710 is a low-VOC, solvent-based adhesive primer for Mapethene LT60/HT60 and is also for vertical and horizontal applications. The primer is quick-drying and improves the adhesion of LT60/HT60 membranes to many substrates.
Water-based: Mapeprime™ 720W is a water-based and non-flammable adhesive primer for Mapethene LT60/HT60. It is also quick-drying and used for vertical and horizontal applications and can be used to attach Mapedrain™ drainage boards or mats to Mapethene™ and Mapeseal 250GC.
Seal Your Entire Building Envelope with Polyglass
Polyglass® U.S.A., Inc. is a leading manufacturer of high-quality modified bitumen roofing and structural waterproofing products and solutions for the building envelope. At Polyglass, we “Seal the Envelope™” with solutions to protect your entire building, from its foundation to its walls and roofing systems.
Contact us today to learn more about our innovative waterproofing solutions.